American Institute of Steel Construction
Workforce development through documentary-style videos and interactions that replicate hands-on work
Project Overview
The American Institute of Steel Construction (AISC) partnered with Artisan to create the Fabricator Education Training Program for employees at steel fabrication companies to become successful general laborers, welders, and fitters.
The AISC member companies faced a workforce conundrum: They were losing talent to other industries that offered more robust and engaging on-the-job training. Few fabricator shops have the resources to formally train employees, and they often resist pulling people out of production to train or be trained.
AISC wanted to develop e-learning modules to support their member companies’ needs. They teamed up with Artisan to develop training that would enable new employees to become productive fast. In our many conversations with experts and our visits to fabrication shops, we learned that steelworkers are a distinct bunch. They challenged us to make courses that feel authentic to the industry and engage employees who do not always thrive in typical educational settings.
The result is a series of documentary-style video modules that follow new hires as they learn the skills and mindsets to succeed in their first 90 days and beyond. Punctuating the videos are knowledge checks that imitate the actions employees must take on the job.
From New Hire to Confident Steelworker in 90 Days
Through video-based modules, learners observe skills at their own pace, so they have the baseline knowledge to practice and master them on the floor.
Engage Learners with Authentic Characters
We filmed real steelworkers as they trained an actor how to weld, read a tape measure, use a crane, cut steel with a torch, and more.
Build Confidence with Work-like Interactions
We designed knowledge interactions that imitate fabrication tasks and checklists to encourage learners to practice skills with supervision at their workstations.
Envision Career Pathways in the Industry
Interviews with new hires and established workers give learners a glimpse of where they can go from here – and advanced modules in welding, reading fabrication drawings, and fitting give them the tools to get there.
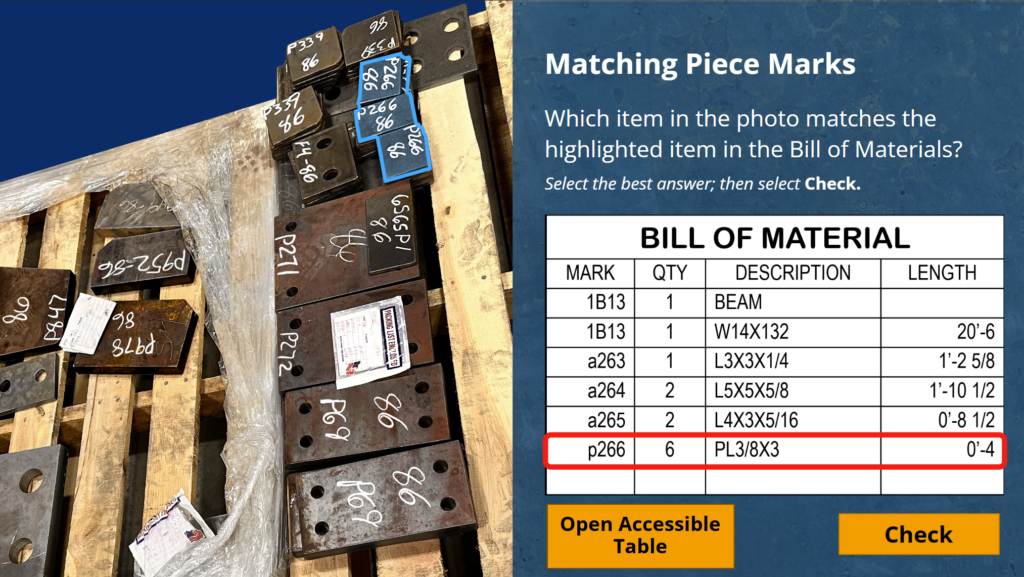
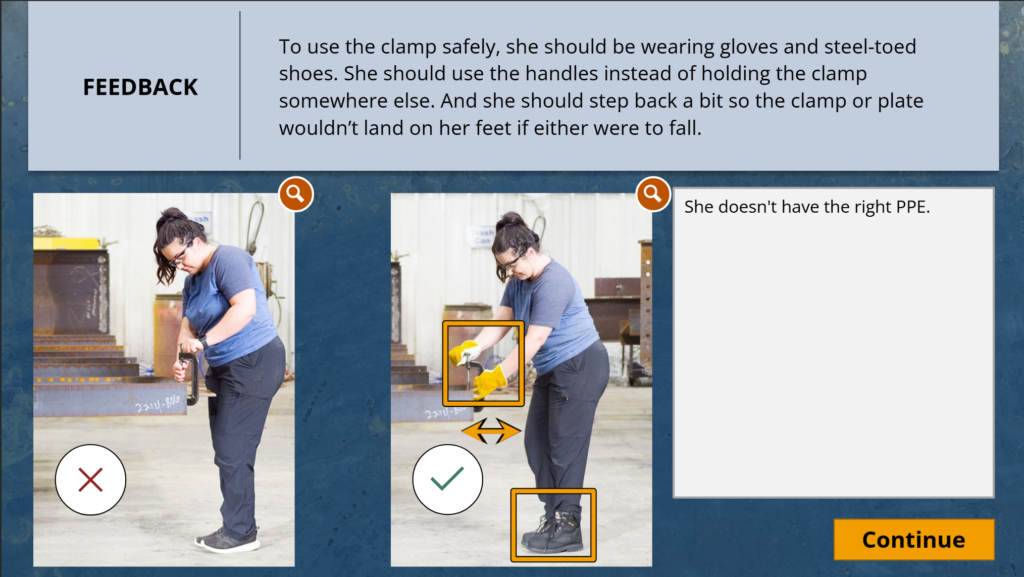
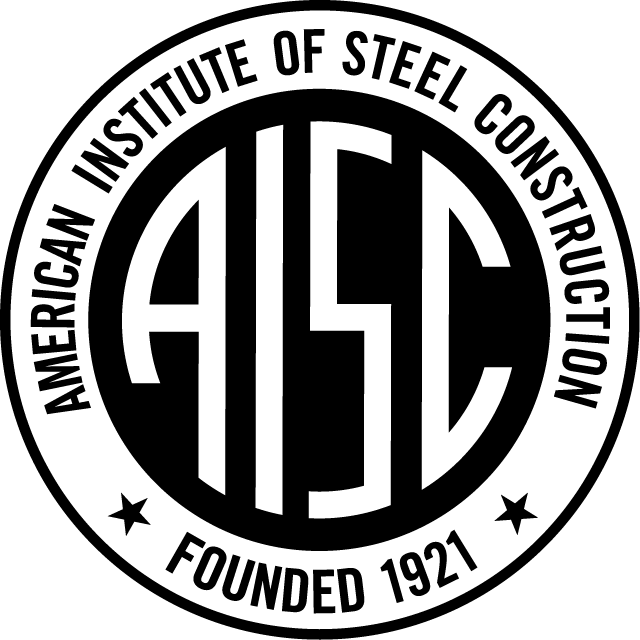
All of us subject matter experts had to back off and let it flow the way Artisan guided us. They would use us as experts but craft the courses in a way that would truly benefit the learner.
– Mark Trimble, AISC senior vice president and former vice president at Huntington Steel in Huntington, WV
Award- Winning
Soon after launching, this project was recognized by learning technology professionals as “Best in Show” at The Leaning Guild’s “DemoFest” competition and was a Bronze winner in the “Online Learning Experience” category in the IELA Awards.